Appendix A 200 mm: the “sweet spot” for industry-relevant microelectronics research in universities
The tool base in the most advanced U.S. university facilities today is designed to handle 150-mm (~6-inch) wafers. The equipment includes general-purpose research tools as well as production tools destined for boutique technologies. A significant portion of the university-installed 150-mm tool base was donated by the Si industry when 200-mm Si wafers (~8 inch) became mainstream in the 1990’s. In a university environment, these tools are often modified to accommodate smaller wafers and odd-shaped samples and thus support a wide range of research programs. The 150-mm tool base in U.S. universities has served academia, industry, and the country well for many years. After three decades, this flexible foundation of general-purpose research tools must be updated and selectively complemented by 200- mm capabilities so that it can support the next generation of discoveries.
Universities have shown repeatedly over the years that industry-relevant research can be carried out with a 150-mm tool set despite industry’s continuing march to 200-mm and more recently 300 mm tools. After all, university research excels when it is of an exploratory nature that thrives on flexibility. University facilities are uniquely equipped to investigate new materials, processes, structures, and devices. In fact, it is often the case that industry reaches out to universities to explore new concepts that they cannot pursue in their more rigid facilities.
The flexibility of the university tool set comes at the price of repeatability, uptime, and performance. Limited repeatability and uptime are a consequence of the instrument age as well as the broad parameter space in which they typically are operated. Also, the capabilities of 150-mm tools are very far from state-of-the-art production 200-mm and 300-mm equipment.
At 200 mm, the balance among economics, performance and flexibility of semiconductor fabrication equipment is far more advantageous for a university environment.
The limited capabilities of the 150-mm tool set particularly hamper universities’ ability to participate in technology translation activities, whether in collaboration with external prototyping foundries or by supporting the advanced development efforts of startups. Success stories do exist but a concerted effort to enhance the relevance of university research and its technology transfer activities calls for a major upgrade in the equipment base of universities.
Given that 300-mm (~12 inch) diameter Si wafer processing is the state-of-the-art today and will remain so for the foreseeable future, it is tempting to think that a few universities in the country ought to entirely bypass 200-mm capabilities and retool their facilities with 300- mm equipment. Surely this approach would dramatically increase the productivity and industrial relevance of university research and expedite technology transfer. However, this simple view clashes, not just with its daunting economics, but also with the flexibility that is the hallmark of a university research environment.
The 300-mm fabrication tools are generally designed for manufacturing throughput and repeatability within narrow process windows. As a result, they are large, highly automated, and extremely costly to acquire and maintain. This is the antithesis of what is desired in a flexible research environment where resources are also at a premium. The narrow usage profile of 300-mm tools makes shared use among a wide range of users very difficult. Even if the facilities and associated support services could be provided on a university campus, the economics of operating a 300-mm university facility are untenable.
At 200 mm, the balance between the economics, performance, and flexibility of semiconductor fabrication equipment is far more advantageous for a university environment. The first consideration is that 200-mm wafer fabs are the preferred manufacturing environment for many commercially important families of products such as ICs based on legacy nodes (for automotive, industrial, and power markets, among others), specialty products such as MEMS, smart power, CMOS image sensors, analog, RF, LEDs, and strategic technologies such as 5G and millimeter-wave, GaAs, GaN power electronics, and SiC. Research and innovation carried out in a 200- mm environment is of immediate applicability for many nascent technologies of economic and strategic significance to the U.S. Further, the process capabilities of 200-mm manufacturing tools approach, in many ways, those of 300-mm equipment while being significantly more flexible. This makes it easier to address problems and opportunities of relevance to the leading-edge CMOS nodes. Perhaps of greatest importance, the economics are vastly more favorable for 200-mm tools when compared with 300-mm equipment. If configured to run wafers of smaller diameters and odd-shaped samples, as we believe can be done, their use could be pooled among a large user community making the costs manageable.
The table below gives a sense of proportion of the cost, under current economic models, of outfitting and operating university research facilities equipped with a full suite of 150-mm, 200-mm, and 300-mm tools assuming that an adequate clean-room environment to host these tools is already available. Depending on the configuration, a 300-mm equipment set is six to seven times more expensive than a 200-mm set. Experience shows that the annual cost of maintenance and staffing is about 20% of the tool cost. A six to seven multiplier, therefore, exists here as well. These costs need to be recovered through user fees. Fabrication-heavy research projects typically can afford to devote about 20% of their budget to user fees. This yields a requirement for an annual research base that is essentially identical to the original cost of the tool base with a corresponding number of researchers, as shown in the table.
At 300 mm, a single facility would require an annual semiconductor research volume and involve a number of fabrication-heavy students and postdocs that is at least one order of magnitude larger than what any U.S. university has ever managed. On the other hand, a few well-equipped 200-mm facilities across the country are entirely feasible. In addition, the enhanced capabilities offered by a flexible high-performance tool set provide a substantial collateral benefit on other disciplines that also contribute to the pool of knowledge, innovation and workforce.
With enhanced collaboration between university researchers and semiconductor tool companies, a small number of selected 300-mm “alpha-tools” (special-purpose research-oriented equipment) would be possible to accommodate within a well-equipped and maintained 200-mm facility. This will speed up technology transfer to 300-mm production tools in industry. Since these alpha tools are unlikely to be shared among a large population of users, appropriately managing them in a university environment will require the careful definition of research and development programs in close partnership with industry and the leadership of a faculty member that has a significant stake in their success.
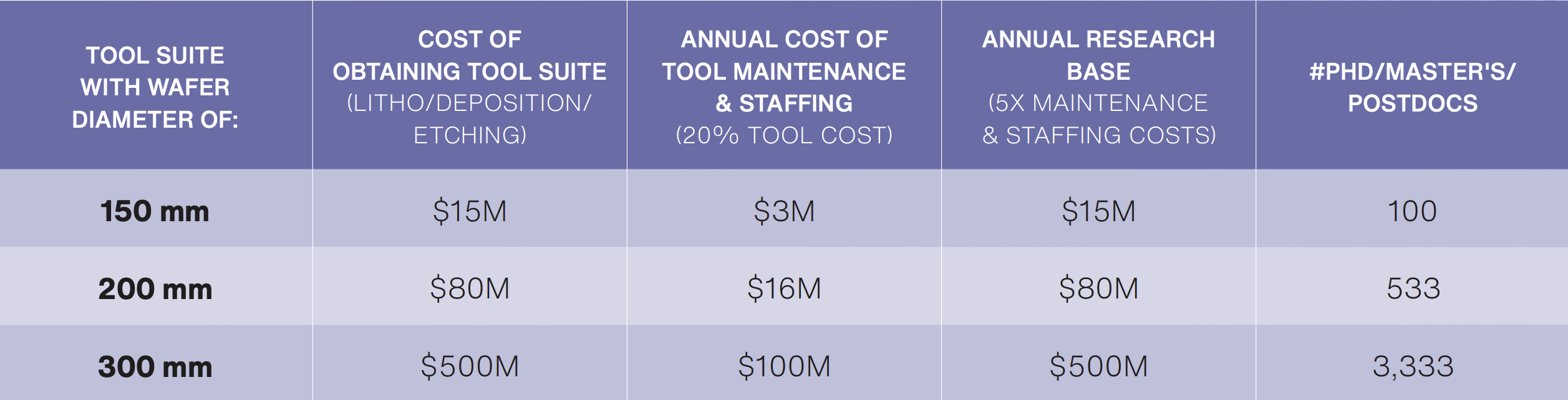